Category Archive: Uncategorized
When 3D printing was first developed in the 1980s, it was primarily used for proof-of-concept models or initial prototypes. Early limitations in technology and materials meant that 3D-printed parts were rarely suitable for field testing or production. However, the past decade has brought rapid advancements in additive manufacturing. These advancements have allowed for more sophisticated materials, faster product development, customization, and greater design freedom.
Modern-day 3D printing has streamlined product development cycles and design iterations. In sectors like die casting, 3D printing is often used to test working models for fit and function before full-scale production begins. The technology helps die casters bypass the costly and time-consuming aspects of creating and testing dies.
However, parts created through 3D printing are susceptible to the same porosity that plagues those created through more traditional processes. Porosity is inherent in the properties of the material and technology. These tiny voids or imperfections can weaken parts and lead to leaks. Although porosity may not be fully eliminated within the 3D print process itself, it can be effectively sealed through vacuum impregnation.
This guide will discuss how vacuum impregnation solves porosity issues in 3D-printed parts, reveal common applications for vacuum impregnation, and clarify misconceptions about the process.
What Causes Porosity in 3D-Printed Parts?
Porosity refers to microscopic voids or defects that form during the 3D printing process. These occur due to incomplete fusion between material layers or trapped gases during melting and solidification. In metal additive manufacturing, such as laser powder bed fusion (LPBF), porosity can seriously compromise mechanical integrity.
There are two primary types of porosity:
- Lack-of-fusion porosity (LoFP). Caused by inadequate melting between layers, LoFP leads to gaps or discontinuities in the material structure.
- Gas-entrapped pores (GeP). Resulting from gas bubbles trapped during the melting process, GeP remain embedded in the final part.
In addition to reducing the durability of 3D-printed parts, these voids can make components unsuitable for pressure-sensitive or high-performance applications. Porosity can also affect surface finish and dimensional accuracy.
In applications that require pressure-tight parts, even microscopic leak paths can cause catastrophic failure in the field. Moreover, certain industries, such as aerospace and medical devices, maintain strict quality control standards that do not accept hidden defects. In these industries, knowing how to seal 3D-printed parts effectively is critical.
How Vacuum Impregnation Seals and Strengthens 3D-Printed Parts
Vacuum impregnation is a proven solution for sealing porosity within 3D-printed components. The process involves placing the part in a vacuum chamber and introducing a liquid resin or sealant that fills micro-voids inside the material. As the sealant cures, it bonds within the part’s internal structure. The process of vacuum impregnation has been shown to significantly improve multiple aspects of 3D prints, including the following:
- Leak resistance
- Mechanical strength
- Chemical resistance
- Dimensional stability
- Surface integrity
All of these benefits are what make vacuum impregnation ideal for functional prototypes, end-use parts, and any other application where consistent performance is critical. Proper resin selection, vacuum pressure control, and curing time are essential for ensuring full impregnation and maximizing part performance.
Two common material types that benefit from vacuum impregnation include:
- Plastics. Nylon and acrylonitrile butadiene styrene (ABS) are frequently used in 3D-printed projects. ABS is cost-effective and suitable for mechanical parts, while nylon offers durability for more complex, functional components.
- Sintered metals. These small components are often used in applications that require high strength and complexity, especially when traditional machining is not feasible.
In addition to increasing strength in 3D-printed parts, vacuum impregnation contributes to sustainability. By sealing internal defects, manufacturers can reduce scrap rates and extend the useful life of parts, which minimizes material waste and energy consumption during production. This makes vacuum impregnation an environmentally responsible post-processing method that aligns with green manufacturing principles.
Common Applications for Sealing 3D-Printed Materials
Here are the main reasons for sealing 3D-printed parts via vacuum impregnation.
Seal Leak Paths
Even highly optimized 3D-printed parts typically achieve a density of about 98-99%. That remaining 1-2% of micro-voids is enough to cause fluid or gas leaks. For applications requiring airtight or watertight performance, such as aerospace components, cooling channels, or sensor housings, sealing this porosity is essential.
Improve Part Integrity
Because 3D-printed parts aren’t as dense as machined parts, they often lack comparable strength. Vacuum impregnation reinforces these parts by bonding internal layers and increasing structural density. As the sealant cures, it enhances layer adhesion and contributes to a more robust part.
Eliminate the Risk of Blooming
Blooming is a condition where the 3D-printed part swells as layers absorb fluids. This not only affects visual appearance but can degrade performance. Vacuum impregnation eliminates this risk by filling the voids where fluid would otherwise accumulate.
In addition to improving performance, vacuum impregnation can increase confidence in the manufacturing process. Engineers can validate prototype designs knowing that material limitations, such as porosity, can be managed effectively. This shortens the timeline between prototyping and production, saving development time and costs.
Misconceptions About Sealing 3D-Printed Parts
Several misconceptions persist about vacuum impregnation in 3D printing. Let’s go through them.
1. Does Vacuum Impregnation Remove Build Lines?
No. Build lines result from the layer-by-layer deposition of material and are part of the surface texture. Build lines are only a concern if the part is intended for cosmetic applications. Vacuum impregnation addresses subsurface porosity, not surface appearance.
2. Does Vacuum Impregnation Seal Surface Defects?
No. Surface cracks or cosmetic flaws aren’t sealed because vacuum impregnation works within the material structure. Only the impregnation sealant that has been drawn into the walls by the force of the vacuum and pressure remains in the part. For visual defects, other post-processing methods like sanding or coating are more suitable.
3. Does Vacuum Impregnation Increase Part Thickness?
No. The process occurs below the surface and does not affect the part’s external dimensions. This makes it suitable for precision applications where tight tolerances are required. Vacuum impregnation is designed to integrate seamlessly into existing workflows. The process is non-destructive and can be automated for high-volume production, making it ideal for industries looking to scale 3D printing without compromising quality.
Why Godfrey & Wing Is the Trusted Name in Sealing 3D-Printed Parts
Established in 1948, Godfrey & Wing is the world’s longest-serving and largest provider of vacuum impregnation services, equipment, and sealants. With a legacy of innovation and precision, we help manufacturers across industries enhance the performance and reliability of their components, 3D-printed and otherwise.
We work closely with engineers and manufacturers to develop tailored solutions for their applications. Whether your priority is sealing micro-porosity in functional prototypes or reinforcing structural integrity in final-use parts, our team can help you implement vacuum impregnation with minimal operational disruption and maximum results.
Whether you’re prototyping a new part or preparing for scaled production, sealing with vacuum impregnation ensures your parts meet the highest standards of strength and reliability. To learn more about our process or to get started on your solution, contact us today.
Porosity is any void or hole in, or on, a casting and is caused by gas formation or solidification shrinkage that occurs while the metal solidifies. If the casting needs to be pressure tight, porosity can allow gas and fluids to seep from the part. In this blog, we will discuss the difference between gas and shrink porosity and the best solution to seal porosity.
What Is Gas Porosity?
One of the most prevalent types of die casting defects is gas porosity, which occurs when rounded air pockets or voids form within or on the surface of the casting. While minor levels of porosity may be allowable for non-critical parts, gas entrapment can ultimately compromise the quality and integrity of critical parts for high-strength applications. Because of this, manufacturers must detect and address porosity promptly in adherence with industry standards.
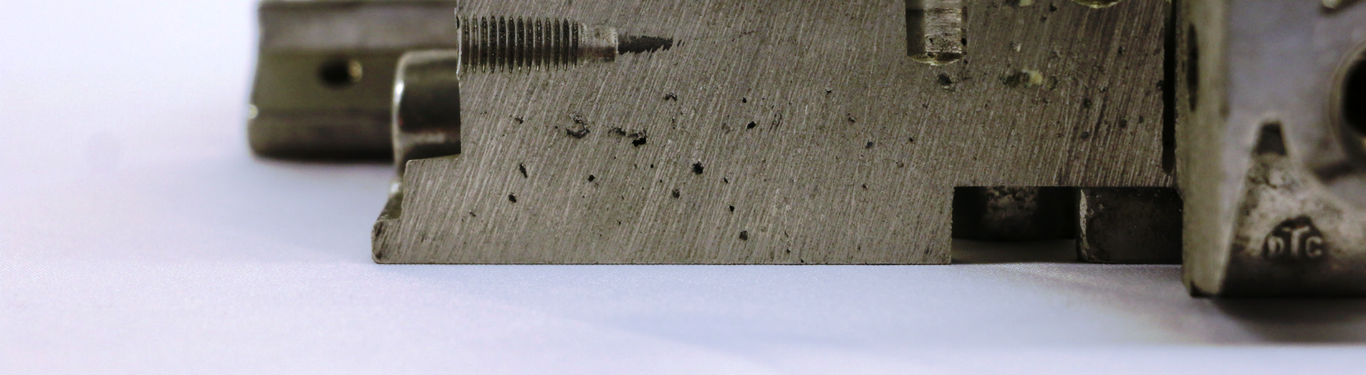
Types of Gas Porosity Defects
There are several different types of gas porosity defects. These include:
- Blisters. Raised defects that form on the surface of the casting.
- Blowholes. Larger round-shaped gas bubbles that form inside the casting and can be difficult to detect without specialized equipment.
- Open holes. A variant of blowholes that form on the surface of the casting.
- Scars. Shallow open hole defects that are typically non-centric.
- Pin holes. Tiny subsurface holes that form in groups in the casting.
- Sand blows. These are large voids that tend to form in the upper portion of the casting.
What is Shrinkage Porosity?
Shrinkage porosity defects are cavities that form when a casting solidifies inside the tool, but there isn’t enough liquid metal to fill the newly formed voids. These have angular surfaces and are different from air entrapment holes, which have rounded shapes.
Shrinkage porosity can cause material weakening. If on the surface, this porosity can lead to lower corrosion resistance as well as a worsened aesthetic appearance. Identifying the size, shape, and position of cavities is essential to determine which defect is occurring and what is causing it to occur.
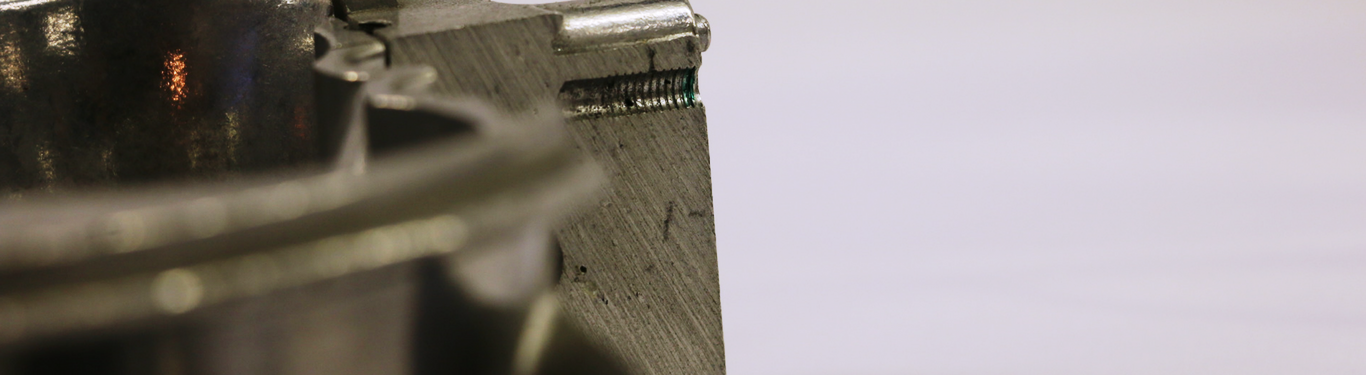
Types of Shrinkage Porosity Defects
There are several different types of shrinkage porosity defects, including:
- Closed shrinkage. These defects form within the casting and typically occur at the top of hot spots.
- Open shrinkage. These defects are visible on the surface of the casting and either have caved surfaces or “pipes” that extend into the casting itself.
- Sponge shrinkage. These thin defects are typically found in the casting’s mid-section.
- Filamentary shrinkage. These form a network of cracks or lines within thick sections of material.
- Dendritic shrinkage. These are narrow, random cavities or fractures. Unlike filamentary shrinkage, these are often unconnected.
Problems of Porosity in Castings
As the amount of porosity increases in an aluminum or iron casting, it can become interconnected and create a leak path. The porosity makes the casting unusable for holding pressure in applications like pumps, compressors, transmissions, and plumbing fixtures.
How to Stop Casting Porosity
The most economical and successful approach to stop casting porosity is through vacuum impregnation. Vacuum impregnation is a method that seals the casting. To complete this process, the impregnating sealant is introduced into the voids within the wall thickness of the casting through vacuum and/or pressure methods.
This method is a cost-effective and permanent solution to casting porosity. Additionally, there is no limit to the size of castings that can be impregnated. Since the impregnation process occurs within the part, it will not distort, discolor, or affect the casting.
Why Godfrey & Wing Is the Solution to Casting Porosity
With first-time-through (FTT) recovery rates of over 99%, Godfrey & Wing’s vacuum impregnation equipment provides an effective and economical solution for stopping casting porosity. We build our systems around OEM’s parts sealing requirements to ensure leak-free and pressure-tight casting.
Die casting is a metal casting process that involves injecting molten metal into a die using high pressure. Die casting facilitates the production of hundreds or thousands of pieces with high dimensional accuracy and a good surface finish, making it highly economical; however, maintaining quality and consistency at such high volumes comes with its own challenges. Manufacturers need to account for porosity, or the tendency for die castings to have voids or holes that cause surface-level flaws. Read on to learn more about die casting porosity, problems it can cause, and how vacuum impregnation seals die casting porosity.
What Is Die Casting Porosity?
Die casting porosity refers to specific defects found within the casting. Two of the most common types of porosity in completed metal goods are gas porosity and shrinkage porosity. Gas porosity is often caused by trapped air or other gases during solidification. It is always buoyant, meaning the resulting bubbles are typically found near the top of the casting (as seen below).
Shrinkage porosity, on the other hand, refers to internal voids that can form as the metal cools. This is because the solid metal volume is less than the volume of liquid metal at higher temperatures. Shrinkage porosity has a linear or jagged appearance and tends to occur in either the drag or cope portion of the casting (below the surface).
In addition to the above, having too much die lube can also contribute to porosity in die casting. While die lube is essential for removing cooled goods from the molds, too much can interfere with solid formation and create surface-level flaws.
Why Is Porosity a Problem?
While porosity is inherent in die casting manufacturing, it can impact part performance, especially in applications where pressure integrity is a vital characteristic. Far from just being an aesthetic or durability problem, die-cast porosity can lead to early breakdowns or even failures. Consider the following examples:
Blind Porosity
Blind porosity creates gaps that sit along the surface, pushing slightly into the interior but not creating uninterrupted passages for liquid to seep in. Manufacturers can expose blind porosity during the finishing stages. While it doesn’t make goods mechanically weaker, it does increase the risk of corrosion. The pores can also hold onto cleaning chemicals from powder coating or anodizing pre-treatments and then leach out after treatment, causing blemishes on the surface.
Through Porosity
Through porosity creates a leak path that runs through casting walls, or can be exposed after machining. This can weaken the metal and make it unsuitable for applications that require excellent pressure tightness, such as automotive and marine applications. Through porosity may make components weaker, create failure points, and prevent parts from reliably holding fluids.
Fully Enclosed Porosity
These pores are completely enclosed and don’t create leak paths. However, fully enclosed pores can become problematic if they’re exposed during surface finishing.
How to Fix Die Casting Porosity
Manufacturers can significantly reduce or completely eliminate failures due to die casting porosity with the right equipment and processes. One of the most effective methods is vacuum impregnation. With this controlled method, manufacturers use vacuuming and pressure to introduce the impregnating material into the voids, sealing the voids to make the casting fit for pressure-sensitive applications.
Benefits of using die casting vacuum impregnation include:
- A fast, cost-effective seal that doesn’t impact the component’s physical properties or functionality
- No residual contamination or leaching
Manufacturers can use vacuum impregnation for castings of any size, creating a permanent seal as well as a more consistent look, feel, and functionality in finished products.
Why Godfrey & Wing Is the Trusted Solution for Die Casting Porosity
At Godfrey & Wing, we specialize in closing the gaps left by die casting processes. Our equipment can provide fast, cost-efficient, and thorough vacuum impregnation processes to address porosity in die casting manufacturing. We’re committed to building systems that create effective, reliable seals that meet or exceed OEM requirements, and our team has decades of experience researching and improving solutions for die cast porosity.
Contact us today to learn more about our products and services.
Godfrey & Wing, a leading global manufacturer of vacuum impregnation technology, has received a contract for an Advanced Graphite Impregnation (AGI) system from a hydrogen fuel cell manufacturer. Starting in 2023, the system will seal leak paths in bi-polar plates in fuel cell stacks for fuel cell vehicles (FCV).
The AGI is designed from Godfrey & Wing’s , which is the world’s most widely used impregnation system. While the HVLV was originally designed to seal leak paths in die cast aluminum, the AGI seals leak paths in graphite parts. A modular system, the AGI seals graphite leak paths while keeping parts clean. With a small footprint of 116 square feet, it can fit in the production line to achieve continuous production flow. In addition, the AGI will be equipped with custom fixtures to remove the risk of part damage and contamination.
While FCVs operate on electricity and are zero-emission, they do so differently than battery-powered Electric Vehicles (EV). In an FCV, hydrogen reacts electrochemically to produce electricity to power the vehicle. Hydrogen fuel cells are designed for use in industries such as transportation, construction, industrial equipment, and others that have traditionally relied on internal combustion technology.
“With a proven record in delivering results for ICEs, we are helping OEMs and manufacturers succeed as they now invest in FCV and EVs.” Said Johnny Halladay, Business Unit Director. “OEMs are moving at a fast pace to build better and cleaner cars. We are excited to help these companies meet their demand.”
Hydrogen infrastructure is growing across North America, and fuel cell transit buses are already in use in the United States and Canada. The global market for fuel cells was valued at $6.6 billion in 2021, according to BCC Research, and is expected to grow at a 20.1% CAGR from 2022 to 2027.
It is expected that there will be 134 electric vehicle (EV) car models available by 2024. Both well-established industry leaders and startups are debuting new car models and redesigning well-known models to be EVs. In addition, these companies are announcing investments to shift from internal combustion engines (ICE) to EVs. This competitive landscape rewards companies that can identify opportunities to adapt appropriately.
(more…)
When it comes to vacuum impregnation, it’s essential to ensure that the parts being impregnated are dry beforehand. This is because any surface impurities can interfere with the impregnation process, leading to subpar results.
If any residual fluids or debris are on the parts prior to impregnation, then the following problems may occur.
Vacuum Pressure Impregnation (VPI) is a method to insulate wound electro-mechanical parts thoroughly with a resin or varnish. VPI is a critical process to insulate and seal the porosity of the parts. VPI is essential to ensure that parts function correctly and improve the longevity of the equipment (Image 1). This blog is a guide that will explain the process, advantages and applications of VPI.
(more…)
The phrase aluminum die casting porosity is used extensively when talking about any void in an aluminum casting, but it does not describe the actual problem. It can take many different shapes and forms, but it is often described just as “porosity”. When analyzing a casting’s porosity, it is important to describe specifics like size, shape, location, and frequency (Image 1). Since porosity is within the casting’s walls, the best way to analyze it is through Nondestructive Testing.
(more…)
One component that engineers are designing in electric vehicles (EVs) is the electric motor. This component is one of the main driving-forces behind EVs. Per IDTEchEx, over 100 million electric motors will be required by 2032. The EV market is constantly evolving with new designs and higher performance requirements to meet these consumer demands. These requirements can result in more parts being rejected and scrapped. Leading to increased costs, and delayed production.
(more…)
Electronics play a crucial role in electric vehicles (EVs). In 2000 automobile electronics were responsible for 18 percent of the cost of a car. Twenty years later, electronics accounted for 40 percent of a car’s cost. The use of electronics will continue to meet fuel efficiency, safety regulations, and consumer standards. However, while the use of electronics will grow, manufacturers must ensure their parts’ quality, safety, and their bottom line’s integrity.
(more…)
Page 1 of 1112345...10...»Last »