It is expected that there will be 134 electric vehicle (EV) car models available by 2024. Both well-established industry leaders and startups are debuting new car models and redesigning well-known models to be EVs. In addition, these companies are announcing investments to shift from internal combustion engines (ICE) to EVs. This competitive landscape rewards companies that can identify opportunities to adapt appropriately.
The Challenge
One example is a multinational automotive manufacturer developing an EV model for one of its sport utility vehicles (SUV). This SUV model has a passionate customer base. These customers view themselves as a community that loves adventure and is environmentally conscious. An electric SUV would align with their values.
The electric SUV model requires two batteries per vehicle (Image 1). During testing, the OEM discovered coolant leaking from a high percentage of the battery tray die castings. This threatened to be disastrous, affecting the assembly of thousands of vehicles. If the OEM could not find a solution quickly, they would need to shut down production and would lose revenue.
Image 1: The OEM discovered coolant leaking from a battery tray casting for a new SUV.
The OEM contacted Godfrey & Wing, having used its vacuum impregnation technology as part of its manufacturing of die cast aluminum parts and components.But while vacuum impregnation is a viable solution for sealing die castings, it didn’t seem to be viable for these battery assemblies. While the process could indeed seal the discovered leak paths, multiple complications would arise.
- Sealant contamination. Excess cured sealant would affect assembly and part quality.
- With traditional vacuum impregnation processes, an entire part is submerged in sealant and water. Some electrical components would be incompatible with the sealant, water, or heat that are part of the impregnation process (Image 2). This would result in part damage.
Image 2: Some electrical components would be incompatible with the sealant, water, or heat from traditional vacuum impregnation process
Disassembly and reassembly of the batteries—needed for the vacuum impregnation process—would delay production and risk damaging fragile electrical components.
The Solution
To determine how impregnation could be most effective, Godfrey & Wing conducted controlled tests with sample batteries. The testing discovered leak paths that had formed in the battery’s die-cast aluminum housing. The company tested multiple processes and sealants to determine the best seal rates without damaging any components.
Godfrey & Wing’s research determined that the best process and sealant would be:
Single-point Impregnation — Godfrey & Wing developed a patent-pending process called single-point impregnation. The process is in accordance with MIL-STD-276A Method A. Single-point impregnation comes in contact with only the leak path. The rest of the battery’s components are untouched, which eliminates the risk of sealant contamination.
Image 3: Only the leak path encounters the sealant.
This eliminates the risk of sealant contamination since no other components are touched.
Internal Pressure Process — All openings are plugged, except for the ports used in the leak path. Sealant is then impregnated with pressure into the part through the port (Image 3).
95-1000AC sealant — This sealant is anaerobic, meaning it cures in the absence of air with no heat or water. Using this sealant protects battery components that are incompatible with heat and water.
The testing and development of the process was done expeditiously, in less than two weeks. With a proven solution, the OEM moved forward with sealing its production parts.
Godfrey & Wing processed the parts inside of shipping containers. This expedited the production process and removed the risk of handling damage. The operator connected an inlet and outlet tube to each battery (Image 4). The sealant flowed through the tube to impregnate any leak paths. A pulsating rinse then flowed through the tube to wash excess sealant out of each part.
Image 4: The operator connected an inlet and outlet tube to each battery while the parts are in the shipping containers.
This expedited the production process and removed the risk of handling damage.
The Results
Once the process was developed and approved, Godfrey & Wing built the system and began processing production in two weeks. The solution answered the manufacturer’s challenges:
Seal leak paths — Godfrey & Wing’s solution sealed 99.98% parts. This allowed the manufacturer to return parts to production without losing productivity.
Achieve part performance — The internal pressure impregnation and anaerobic sealant protected critical features, allowing the batteries to function as designed.
In Summary
As the demand for EVs continues, so too will the demand for innovative and adaptive manufacturing processes. By working with Godfrey & Wing, this manufacturer found a solution to a potentially catastrophic problem in four weeks. Through research, Godfrey & Wing’s single-point impregnation process is the best and most economical option to meet the OEM’s quality and production demands.
The EV market has unprecedent competition. By having a partnership with Godfrey & Wing on sealing leak paths, this manufacturer has an advantage over its competition.
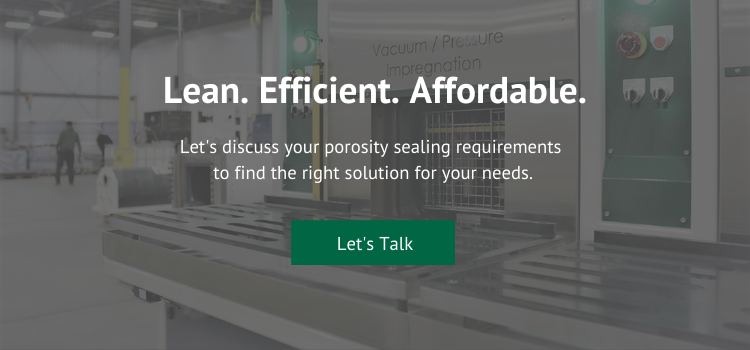