When it comes to vacuum impregnation, it’s essential to ensure that the parts being impregnated are dry beforehand. This is because any surface impurities can interfere with the impregnation process, leading to subpar results.
If any residual fluids or debris are on the parts prior to impregnation, then the following problems may occur.
Parts Not Being Properly Sealed
The fluids in the leak path will prohibit the process from fully sealing the leak path (Image 1). The parts may not pass the leak test since the leak path is not properly sealed. Any parts that fail the leak test will be unusable and possibly scrapped.
Image 1: The oil left on this part will prohibit it from fully being sealed.
Increase TAKT time
Any residual fluids will need to be boiled off in the vacuum chamber. When water boils, it expands approximately 1,700 times. That expansion means there is more volume for the vacuum pump to evacuate from the vessel, which takes time. In addition, if the water is in the part’s porosity, then the evaporation process could take several seconds more than evaporating from the surface. A few additional seconds may not sound like a lot of time. But this additional time compounds and can cause an increase in production time and costs.
Improper Assembly
Debris in tapped holes or blind passages can cause assembly issues or prevent fluid flow (Image 2). If the debris is not removed, then the parts will not function correctly. Cleaning the debris will require additional steps, which may create production delays.
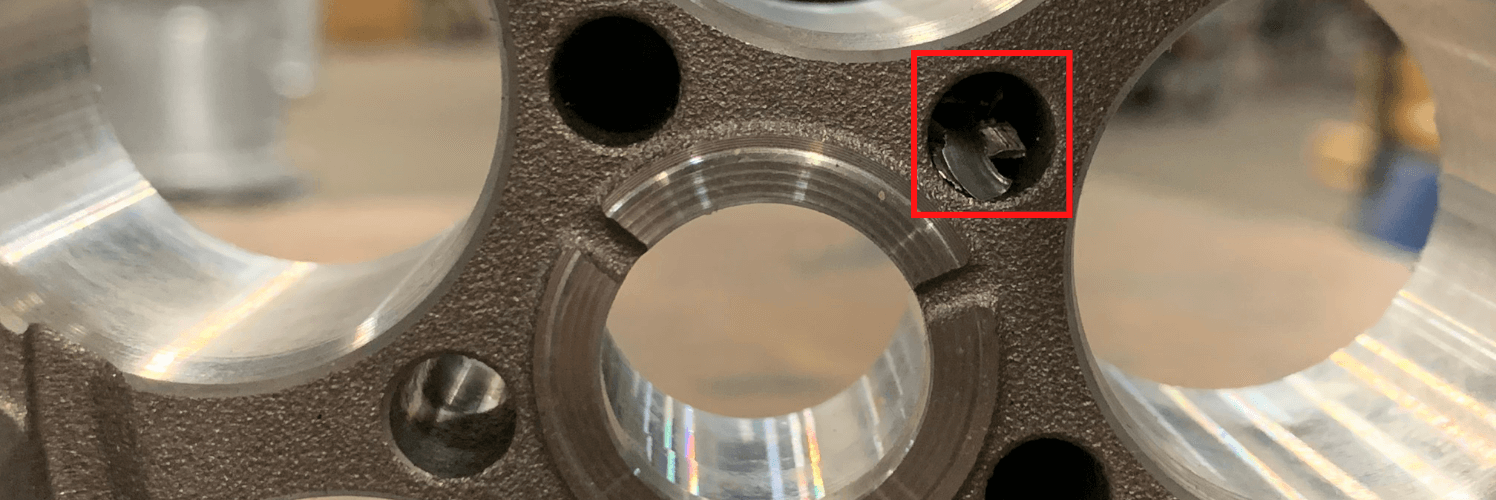
Image 2: the debris in the blind passage (highlighted in red) will lead to assembly issues.
Inhibits Part Rinsing
Debris remaining on and part will inhibit the rinsing during the impregnation process. The debris will prohibit the sealant from fully being washed from the part’s internal passages, taps, pockets and features where sealant is undesirable. Inadequate rinsing will lead to sealant being cured in undesired features that will affect the part’s assembly and quality.
Sealant Contamination
Residual fluids and debris on the part can contaminate the sealant (Image 3). The contamination will affect the sealant’s chemistry causing it to lose chemical properties and significantly reduce the recovery rate. The contamination will also require maintenance to replace the contaminated sealant with pure sealant. This will cause production delays and unforeseen costs.
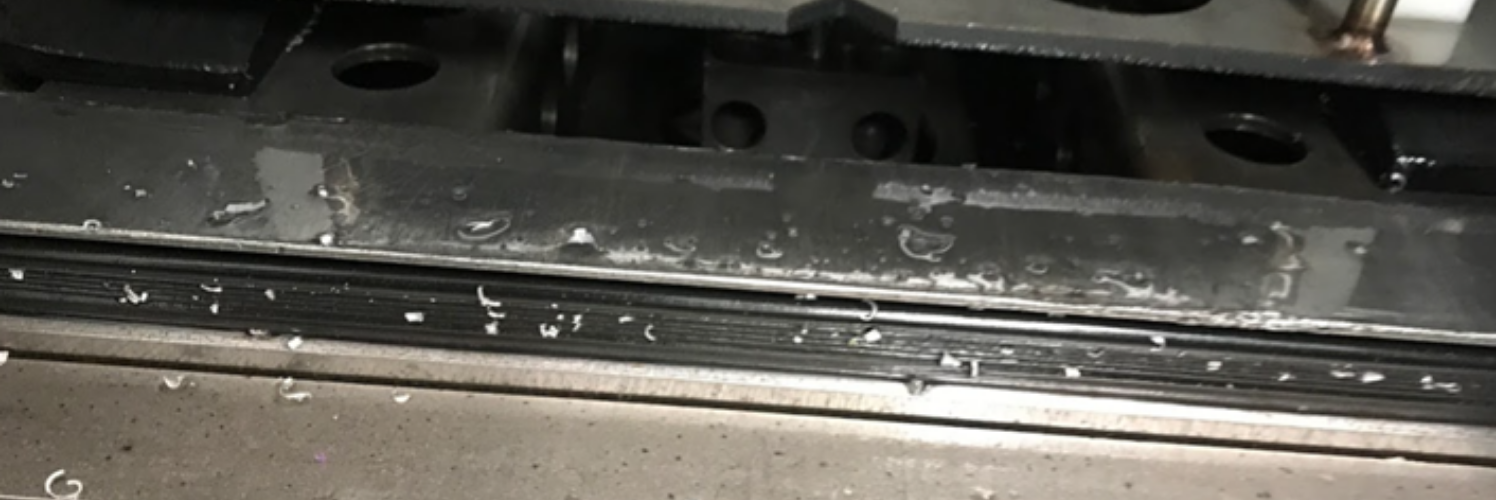
Image 3: The machine chip left on the part will be dragged into the sealant. This will contaminate the sealant, rendering it less effective.
Best Way to Dry Parts
The best way to dry parts is with a vacuum drying system. The equipment allows for efficient and effective sealing, resulting in fewer production delays and costs (Image 4). Using vacuum drying equipment ensures parts are properly prepared for vacuum impregnation.
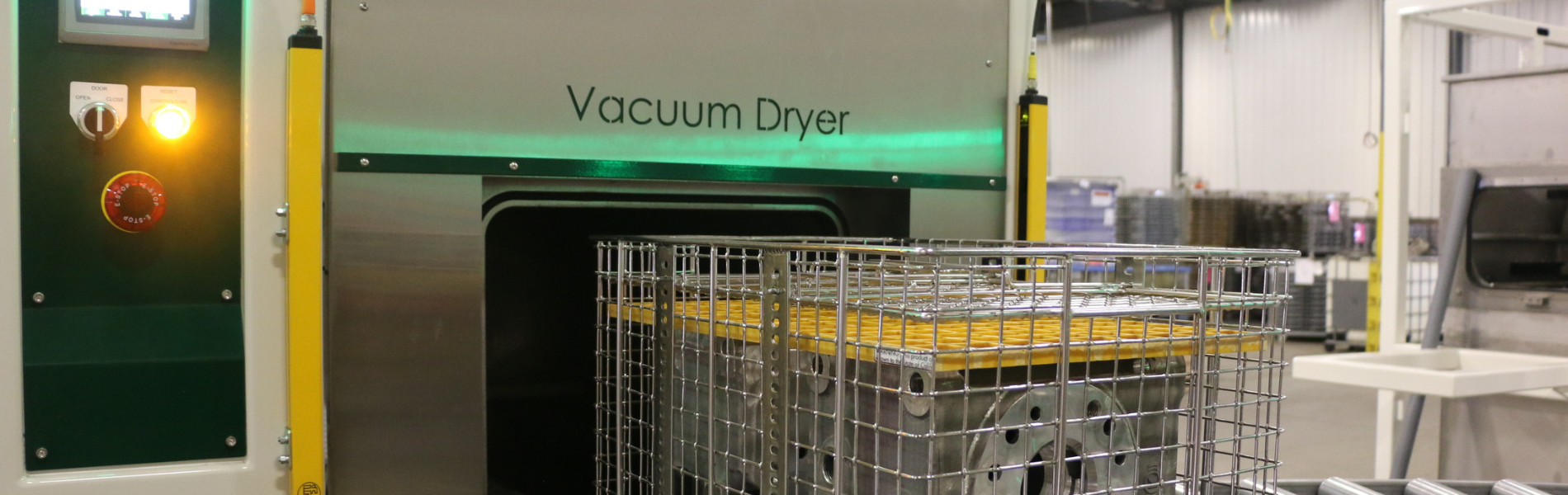
Image 4: Vacuum drying equipment dries parts prior to vacuum impregnation, allowing them to be efficiently and effectively sealed.
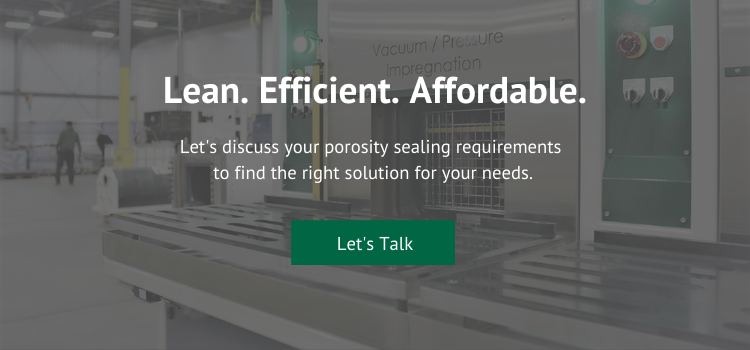