Years ago and even today, Batch System Vacuum Impregnation was the most common vacuum impregnation system. Despite a recent shift towards Single Piece Part Flow (i.e. HVLV, CFI, APi, and EcoSeal), there is still value in Batch System Vacuum Impregnation. Bottom line, the advantages of this process is that it is the best solution to provide capacity-multiple amounts of product can be serviced in one cycle.
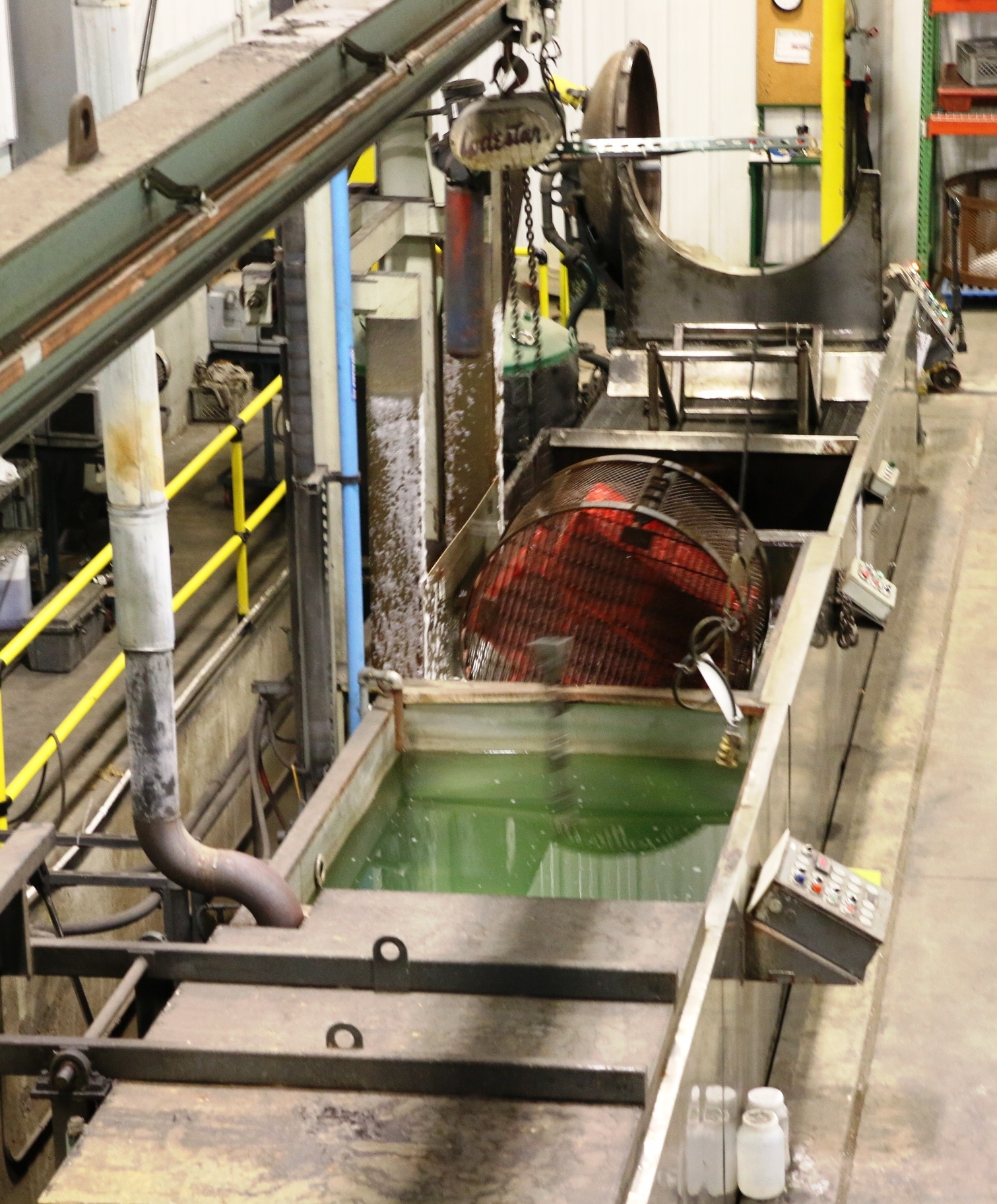
Both batch and single piece part flow impregnation systems accomplish the same 4 basic tasks:
- Penetration of casting porosity/leak paths with sealant
- Recovery of excess sealant from tapped holes, cavities and outside casting surface
- Cleaning of the casting’s surface features to remove undesirable sealant
- Curing the sealant that has been impregnated within the casting walls.
So if all impregnation systems accomplish the same tasks, then how does a batch system work differently?
It’s simple; a Batch system is compiled of a large vessel, large tanks and large baskets.
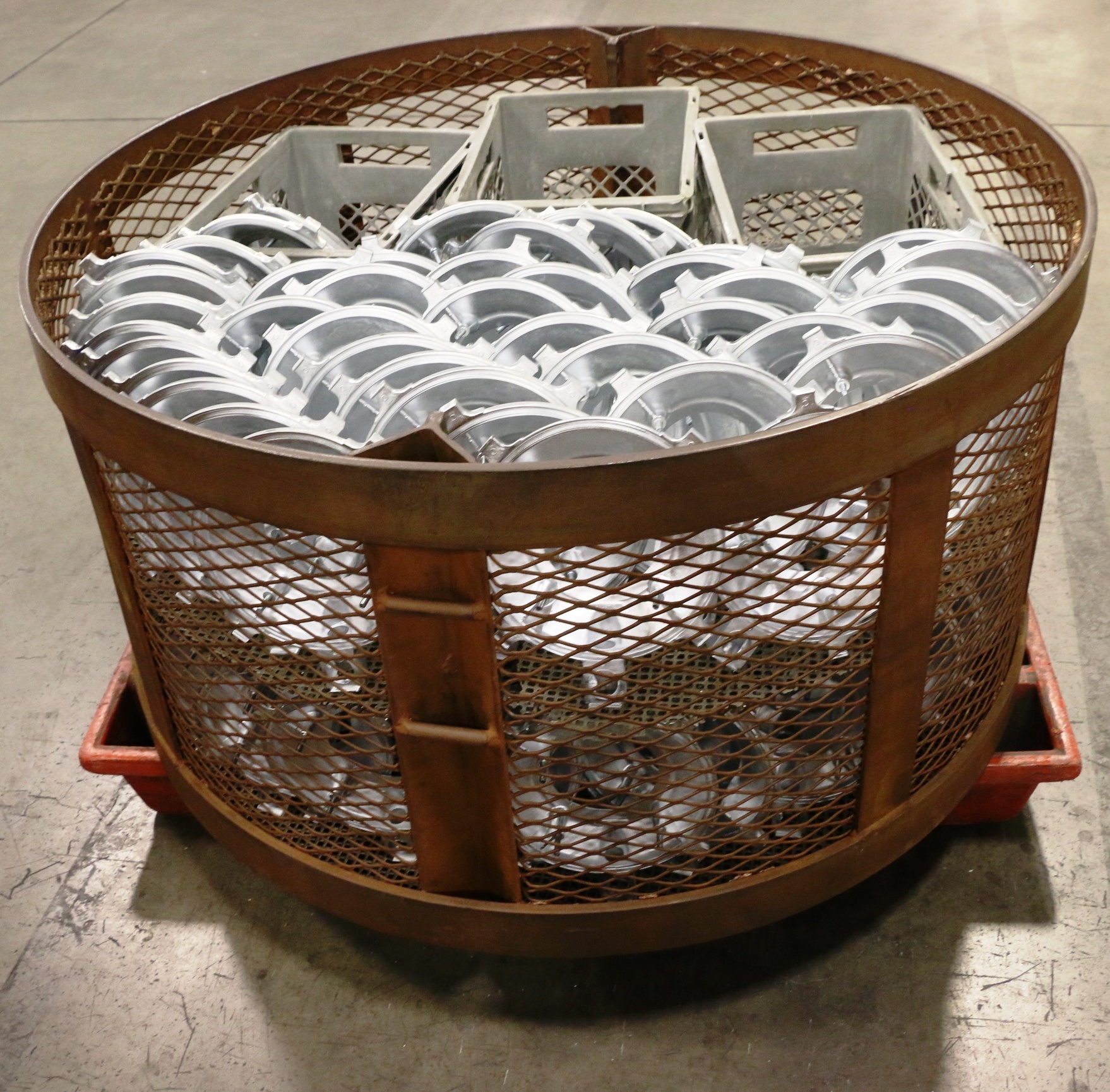
Multiple castings are placed in baskets, which then are put through the impregnation process, first the vessel, then the wash and finally the cure.
So when should a Batch system used? The system should be utilized when:
- Flexibility in range of part sizes and shapes
- Parts that have a more forgiving leak rate
- Large, heavy parts that do not have small blind threaded holes
- High quantity of raw (non-machined) castings where part-on-part contact is not an issue.
This condensed overview will provide you a better understanding on the benefits of a Batch system. Of course, this system is not a “one size fits all” for vacuum impregnation needs. At Godfrey & Wing, we manufacture and utilize both batch and single piece part flow. Both systems have benefits to different needs.
Next Steps
- Talk to us about what services are right to you.
- Understand porosity and vacuum impregnation by downloading our handbook.
- Stay connected and become an expert on porosity and vacuum impregnation by subscribing to our blog.