Electronics play a crucial role in electric vehicles (EVs). In 2000 automobile electronics were responsible for 18 percent of the cost of a car. Twenty years later, electronics accounted for 40 percent of a car’s cost. The use of electronics will continue to meet fuel efficiency, safety regulations, and consumer standards. However, while the use of electronics will grow, manufacturers must ensure their parts’ quality, safety, and their bottom line’s integrity.
Source: Car and Driver
Metal pins and wires are embedded in the plastic housing in these parts. When the parts experience heat during manufacturing, the plastic and metal expand at different rates, creating microscopic leak paths between the materials.
One example are the overmolded pieces in this EV battery. The part needs to be pressure tight, while the leak path is unavoidable, it will result in the part being rejected and scrapped (Image 1).
Image 1: The leak path in this EV battery needs to be sealed so the part can work properly.
The rejected parts will cause a field failure, with an unforeseen increase in cost and loss of production. As a result, the massive expansion of electronics in automobiles has made sealing the leak paths critical. Vacuum impregnation is the most common and preferred method by OEMs to seal electronics.
Here are the three main reasons why:
Seal Leak Paths
Vacuum impregnation is a subsurface process that seals leak paths by filling the void between the two dissimilar materials. If not sealed, then fluids may penetrate the connector. Vacuum impregnation prevents fluids from leaking by sealing the leak paths.
Related Case Study: How Vacuum Impregnation Enables Over Molded Manufacturing
Prevent Corrosion
From either oxidation or galvanization, corrosion reduces current-carrying capacity and causes the part failure. Vacuum impregnation prevents corrosion by sealing the leak path that oxygen and moisture can follow(Image 2).
Image 2: Vacuum impregnation will prevent the metal prongs from corrosion.
Enable Design Freedom
Vacuum impregnation does not change the part’s dimensions, allowing engineers to design and make parts to the net shape. Since the process does not leave any sealant on the part’s surface, an engineer does not need to incorporate dimensional allowance.
In Summary
The surge in electronics in EVs has made leak path sealing crucial. Properly sealing the porosity ensures the component’s quality meets its performance requirements. Vacuum impregnation is the most effective solution for sealing leak paths and preventing corrosion while enabling design freedom.
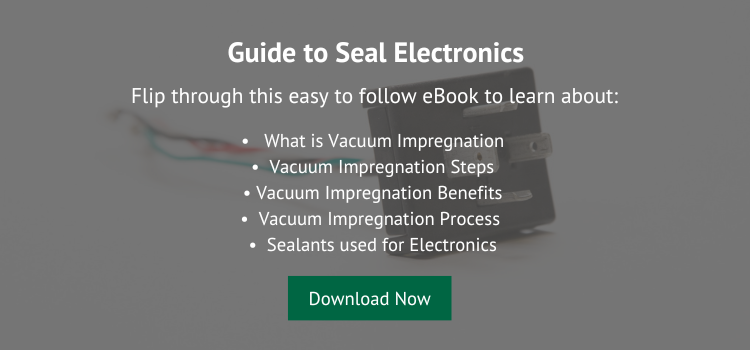