There exists a misconception on testing requirements for vacuum impregnation sealants and vacuum impregnation processes. Testing impregnation sealants for application compatibility and testing the impregnation process effectiveness are grossly different.
Impregnation sealants are tested through Military Standard MIL-I-17563C. MIL-I-17563C demonstrates a sealant is compatible with the application and that the sealant will not degrade or fail over the life of the part.
Impregnation processes are governed by Military Standard MIL-STD-276A. MIL-STD-276A provides the standards for processing to seal parts and testing process effectiveness.
The misconception comes to light as operators or engineers use test methods designed to demonstrate impregnation sealant compatibility as an indication of impregnation process effectiveness. The outcome of this misapplication of testing methods will lead to false positive results. Meaning the impregnation process will appear capable of sealing parts when it is not. This can create a field failure leading to significant unforeseen costs and quality issues.
This blog clarifies the difference between the two specifications, MIL-I-17563C and MIL-STD-276A, and the testing required for each standard.
What is a Military Standard?
In the late 18th century and throughout the 19th century, the American and French militaries were early sponsors and advocates of interchangeability and standardization. Today, the United States Military Standards (often called Mil Specs or MIL-STD), are used to standardize processes and products for the United States Department of Defense. For decades these MIL-STDs have served as the basis for specifications used by global manufacturers to ensure products are manufactured to the same quality standards regardless of their country or point of origin.
Impregnation Sealants: MIL-I-17563C
MIL-I-17563C governs the testing and approval process for vacuum impregnation sealants. Sealants tested must pass this standard to gain acceptance onto the Qualified Product List (QPL).
The specification places impregnation sealants into one of three classes:
- Class 1 – Suitable for service temperatures up to 300°F (149°C)
- Class 1a – Suitable for use on mortar shell castings up to 300°F (149°C)
- Class 2 – Suitable for service temperatures up to 500°F (260°C)
- Class 3 – Suitable for use where air pollution requirements apply and compatible with acrylic-nitrocellulose lacquer paint system up to 300°F (149°C)
MIL-I-17563C Testing
MIL-I-17563C testing is done using a certified test ring. The test ring is used as a ‘carrier’ or ‘standard coupon’ for the sealant testing. The ring has an excessive amount of porosity compared to an actual part. In other words, the sealant in the test ring will be exposed to the maximum amount of cured sealant to the change in fluids, gases, and/or temperatures.
MIL-I-17563C states that the configuration of the test ring should be 1 inch (25.4mm) long with a nominal ¾ inch (19.0mm) inside diameter, and 1 inch (25.4mm) outside diameter (image 1).
Image 1: The test ring shall be 1 inch (25.4mm) long with a nominal ¾ inch (19.0mm) inside diameter and 1 inch (25.4mm) outside diameter.
Test rings shall not have the surface altered by operations such as burnishing, coining or sizing. The interconnected porosity should be 15%-25%. The exact amount is determined by the method specified in ASTM B 328. The alloy composition of the test specimens shall conform to one of the three types as specified in MIL-I-17563C (Table 1).
Table 1: Excerpt from MIL-I-17563C
The test follows five simple steps:
- Pressure Test – Test ring is pressure tested for leakage at 50 lbs./in2 to verify leak paths are present.
- Impregnation – The test ring is impregnated with an approved impregnation process, as discussed below in the “Impregnation Process: MIL-STD-276A” section.
- Pressure Test – After impregnation, the test ring is tested for leakage at 50 lbs./in2. If there is no leakage, then the part is sealed. MIL-I-17563C acknowledges that not all test specimens will pass the leak test after impregnation.
- Environmental Conditioning Test – The test ring is tested as specified on Table 2. This is done to evaluate the sealant’s resistance to fluids, gases, temperatures and time.
- Pressure Test – The test ring is tested again after impregnation. The ring must exhibit zero leakage.
Table 2: Excerpt from MIL-I-17563C
Impregnation Process: MIL-STD-276
MIL-STD-276A is the military approval that governs the impregnation process of porous metal castings and powder metal components. MIL-STD-276A states that there are three viable vacuum impregnation processes: Internal Pressure, Dry Vacuum and Pressure, and Wet Vacuum and Pressure.
Use Parts, Not Test Rings
MIL-STD-276A states that the parts being impregnated are to be used for the process verification. There is no mention of test rings in MIL-STD-276A. As the test rings have little to no similarity to most parts, they are only used to ‘carry’ the sealant, and not test the process. Using the actual part is the only way to measure the process effectiveness, as a pressure test of the part demonstrates the leak path is sealed.
A common misconception is that if one can seal a 15,000 ccm leak rate, then one can seal a <100 ccm leak rate. This is incorrect because each leak path is different. The material, wall thickness, porosity, and size will vary between parts. Process parameters, such as cycle time, pressure, wash cycle, and sealant viscosity, will be different to seal a 15,000 ccm leak rate than what is required to seal a <100 ccm leak rate.
Common Misconception on Sealing Powdered Metal Rings
Many operators or engineers assume that if they can seal a powder metal test ring, then the impregnation process is effective. They assume that if they can seal the large porosity in a powder metal test ring, then they can seal porosity of any size. This is not the case. This misconception can be explained by comparing the properties of a powder metal test ring to an engine block (Table 3).
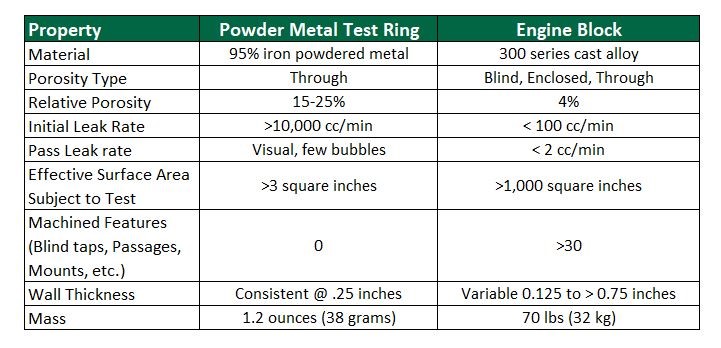
Table 3: Comparing the properties of a powder metal test ring to an engine block.
Most impregnation vessels can impregnate sealant into a test ring that is 15%-25% porous and leaks 10,000 cc/min. A test ring can be impregnated at atmospheric pressure because of the large porosity. Keeping it in requires a passive wash and cure so the sealant does not emulsify out from the leak paths.
Conversely, the engine block requires pressure in the impregnation vessel to penetrate the porosity. This is because the engine block porosity is smaller when compared to the powder metal test ring. Unlike the test ring, the sealant will never wash from the engine block porosity due to the small size of the porosity. However, the sealant must still be removed from small machined features in the block which requires an aggressive wash and cure.
In Summary
Properly understanding the difference between military standards is the first step to identify the best means to seal a leak path. Using the correct sealant and process will ensure that parts are properly sealed and eliminate the possibility of a field failure.