Die casting is a metal casting process that involves injecting molten metal into a die using high pressure. Die casting facilitates the production of hundreds or thousands of pieces with high dimensional accuracy and a good surface finish, making it highly economical; however, maintaining quality and consistency at such high volumes comes with its own challenges. Manufacturers need to account for porosity, or the tendency for die castings to have voids or holes that cause surface-level flaws. Read on to learn more about die casting porosity, problems it can cause, and how vacuum impregnation seals die casting porosity.
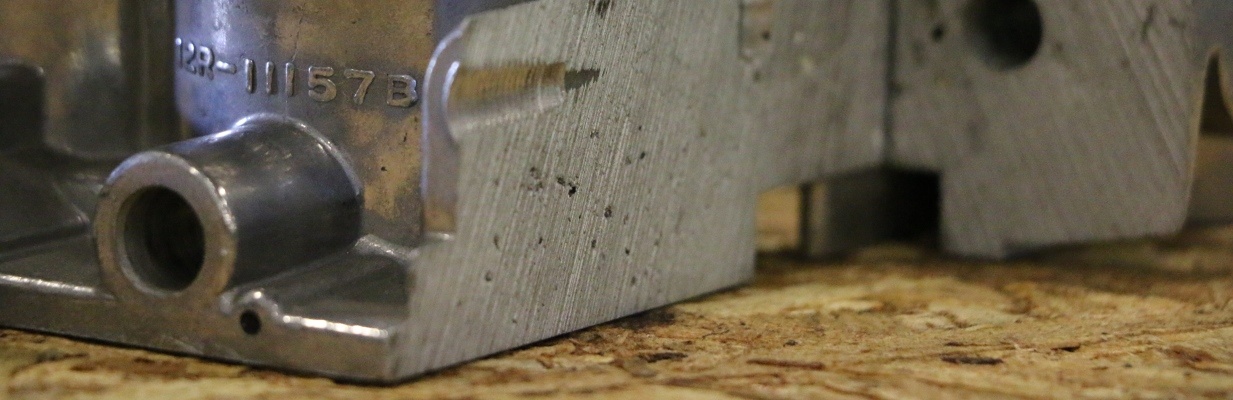
What Is Die Casting Porosity?
Die casting porosity refers to specific defects found within the casting. Two of the most common types of porosity in completed metal goods are gas porosity and shrinkage porosity. Gas porosity is often caused by trapped air or other gases during solidification. It is always buoyant, meaning the resulting bubbles are typically found near the top of the casting (as seen below).
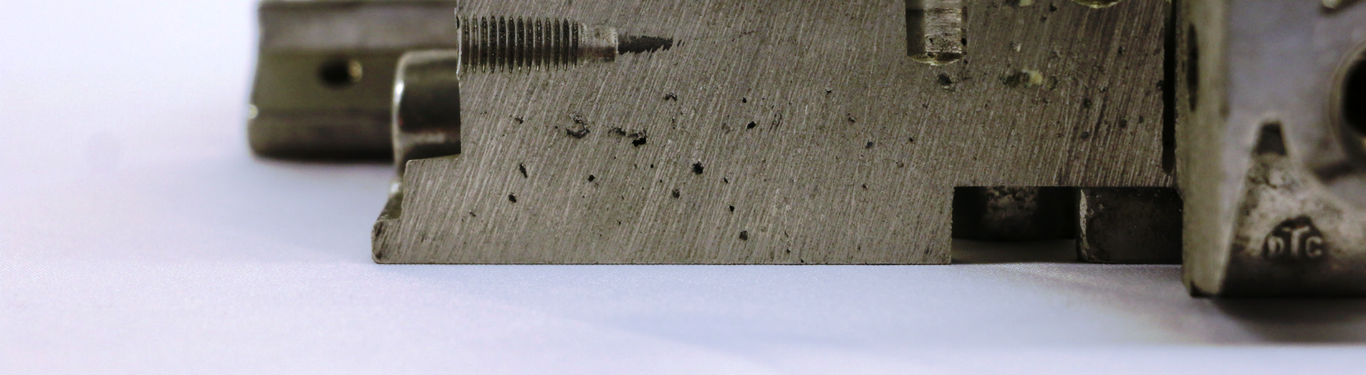
Shrinkage porosity, on the other hand, refers to internal voids that can form as the metal cools. This is because the solid metal volume is less than the volume of liquid metal at higher temperatures. Shrinkage porosity has a linear or jagged appearance and tends to occur in either the drag or cope portion of the casting (below the surface).
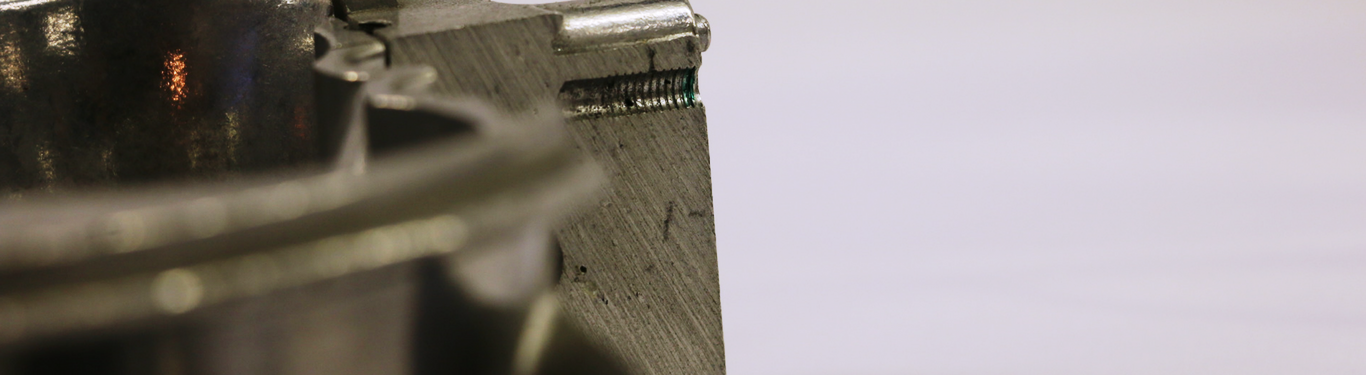
In addition to the above, having too much die lube can also contribute to porosity in die casting. While die lube is essential for removing cooled goods from the molds, too much can interfere with solid formation and create surface-level flaws.
Why Is Porosity a Problem?
While porosity is inherent in die casting manufacturing, it can impact part performance, especially in applications where pressure integrity is a vital characteristic. Far from just being an aesthetic or durability problem, die-cast porosity can lead to early breakdowns or even failures. Consider the following examples:
Blind Porosity
Blind porosity creates gaps that sit along the surface, pushing slightly into the interior but not creating uninterrupted passages for liquid to seep in. Manufacturers can expose blind porosity during the finishing stages. While it doesn’t make goods mechanically weaker, it does increase the risk of corrosion. The pores can also hold onto cleaning chemicals from powder coating or anodizing pre-treatments and then leach out after treatment, causing blemishes on the surface.
Through Porosity
Through porosity creates a leak path that runs through casting walls, or can be exposed after machining. This can weaken the metal and make it unsuitable for applications that require excellent pressure tightness, such as automotive and marine applications. Through porosity may make components weaker, create failure points, and prevent parts from reliably holding fluids.
Fully Enclosed Porosity
These pores are completely enclosed and don’t create leak paths. However, fully enclosed pores can become problematic if they’re exposed during surface finishing.
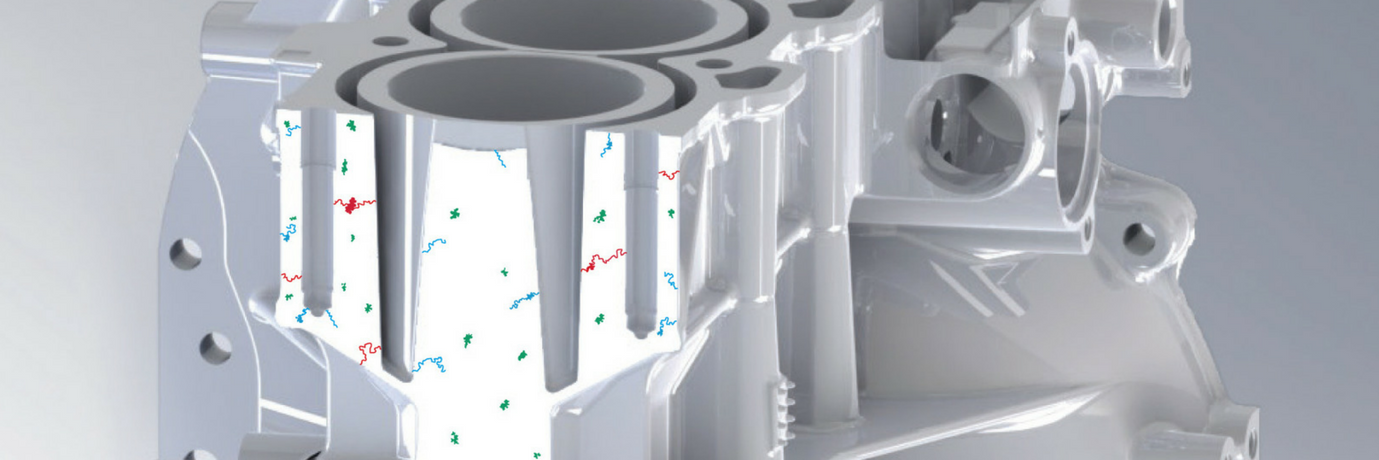
How to Fix Die Casting Porosity
Manufacturers can significantly reduce or completely eliminate failures due to die casting porosity with the right equipment and processes. One of the most effective methods is vacuum impregnation. With this controlled method, manufacturers use vacuuming and pressure to introduce the impregnating material into the voids, sealing the voids to make the casting fit for pressure-sensitive applications.
Benefits of using die casting vacuum impregnation include:
- A fast, cost-effective seal that doesn’t impact the component’s physical properties or functionality
- No residual contamination or leaching
Manufacturers can use vacuum impregnation for castings of any size, creating a permanent seal as well as a more consistent look, feel, and functionality in finished products.
Why Godfrey & Wing Is the Trusted Solution for Die Casting Porosity
At Godfrey & Wing, we specialize in closing the gaps left by die casting processes. Our equipment can provide fast, cost-efficient, and thorough vacuum impregnation processes to address porosity in die casting manufacturing. We’re committed to building systems that create effective, reliable seals that meet or exceed OEM requirements, and our team has decades of experience researching and improving solutions for die cast porosity.
Contact us today to learn more about our products and services.