One component that engineers are designing in electric vehicles (EVs) is the electric motor. This component is one of the main driving-forces behind EVs. Per IDTEchEx, over 100 million electric motors will be required by 2032. The EV market is constantly evolving with new designs and higher performance requirements to meet these consumer demands. These requirements can result in more parts being rejected and scrapped. Leading to increased costs, and delayed production.
In an electric motor, insulated copper wire is wound around a core to create or receive electromagnetic energy, transferring that energy by induction to another coil. Once an electric motor is wound, it must be insulated with a varnish (Image 1). This step is critical to ensure the part’s integrity. Vacuum Pressure Impregnation (VPI) and Varnish Dip are the two most common methods to insulate electric motors.
Image 1: Copper wiring must be insulated to ensure the motor’s performance.
Vacuum Pressure Impregnation Process
During the VPI process, the part is lowered into a pressure vessel, and a vacuum is drawn. As that occurs, a varnish is drawn into the chamber until the unit is completely submerged (Image 2). Pressure is then applied, and the inside and outside of the part becomes thoroughly impregnated with the varnish. Afterward, the part is removed and then cured in an oven.
Air is a critical element that will cause quality and performance issues. Therefore, the vacuum step is crucial to remove the air. This ensures complete varnish penetration.
Image 2: The part is lowered into a pressure vessel, and a vacuum is drawn.
Removing the air is critical to ensure complete varnish penetration.
The Varnish Dip process dips the part into a varnish tank. Afterward, the part cures in an oven. The Varnish Dip process does not have a vacuum component. This means that air is not entirely removed, resulting in the inside and outside of the part not thoroughly impregnated.
Benefits of Vacuum Pressure Impregnation
While both processes have been used for over 60 years, VPI has three significant advantages over Varnish Drip (Image 3).
Improve power output
Because of the vacuum step, VPI varnish has a complete penetration. A fully enclosed part leads to good heat transfer, keeping the electricity within the wires. This results in better motor performance.
Contamination resistance
Contamination penetrates small openings in the unsealed insulation and produces a conducting path between turns or to-ground. As previously stated, VPI fully encloses a part because of the vacuum step. Therefore, VPI ensures no risk of contamination. Air not removed from a part creates microscopic openings that increase contamination risk.
Reduce coil vibration
The most common failure in motors is abrasion. Vibration causes wear and chaffing, leading to a part no longer being able to withstand voltage. Having a part fully enclosed with VPI serves as an adhesive between the motor strands as it turns. This reduces the risk of coil vibration.
Image 3: The VPI process will ensure a parts power output,
improve contamination resistance, and reduce coil vibration.
Image source: Car and Driver
In Summary
Electric motors in EVs offer cutting-edge technology and performance. As the surge of electric motors continues, so too will the need for VPI. Vacuum Pressure Impregnation is the most efficient and effective way to enclose motors. Using VPI ensures part performance while eliminating failure modes.
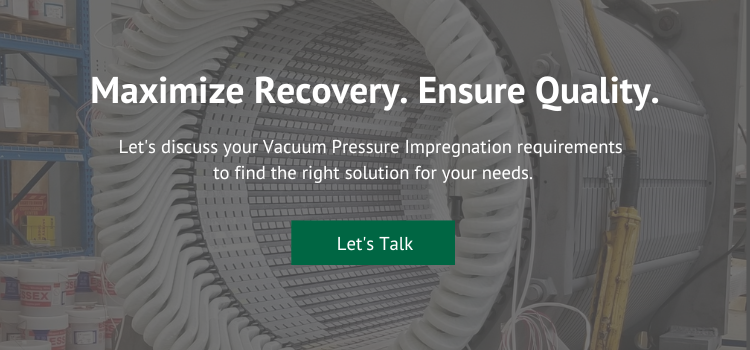