Correcting Three Vacuum Impregnation Myths
Leave a CommentIn some die casting applications, components must also be pressure-tight to hold pressurized fluid or gases. Companies use vacuum impregnation to meet these requirements by sealing the internal leak paths caused by interconnected porosity.
Misconceptions and lack of information about the vacuum impregnation process can hinder its implementation, which may increase unforeseen costs and negatively impact part quality. This piece demystifies vacuum impregnation by correcting three common myths.
Myth: Vacuum Impregnation is a CoatingFact: The process occurs subsurface, with no residual sealant remaining on the part’s surfaces, machine features, blind holes, and taps. Only the sealant drawn into the leak path by the force of the vacuum and pressure remains in the casting.
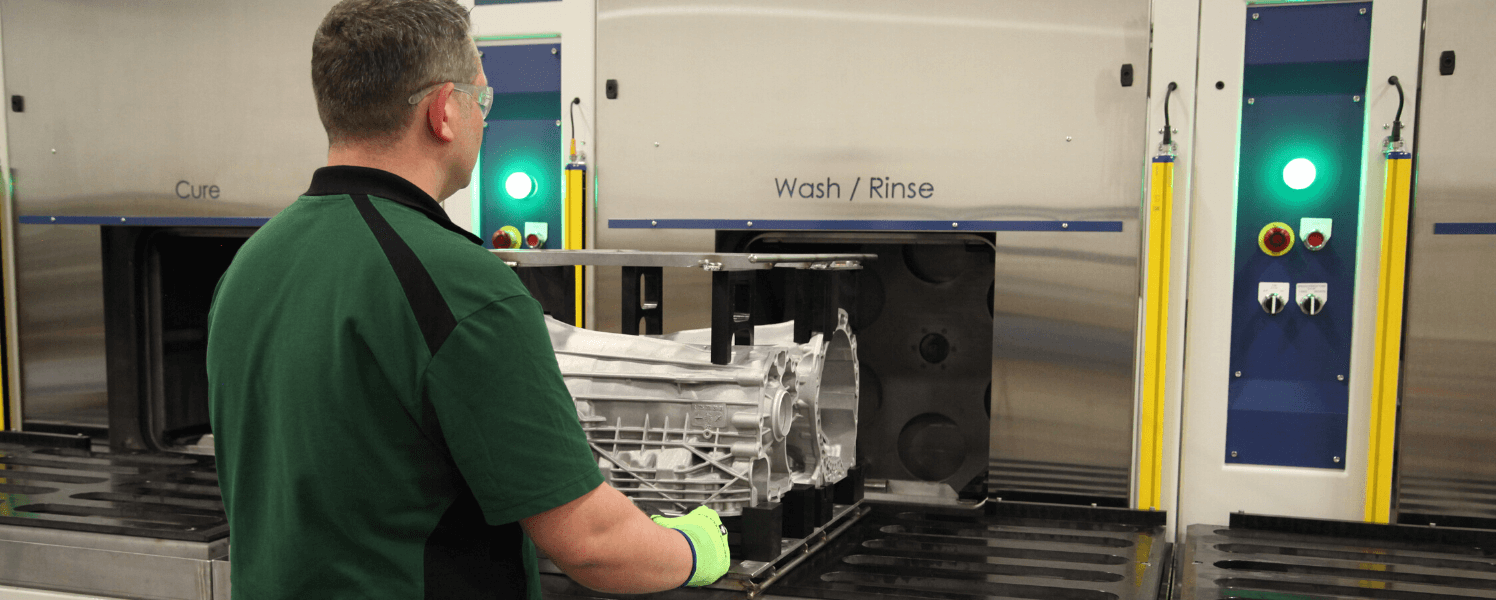
Myth: Vacuum Impregnation Causes Dimensional Changes to CastingsFact: Vacuum impregnation does not change the casting’s dimensions, thus allowing engineers the freedom to design and make parts to the net shapes. Since the vacuum impregnation process occurs subsurface, an engineer does not need to incorporate dimensional allowance.
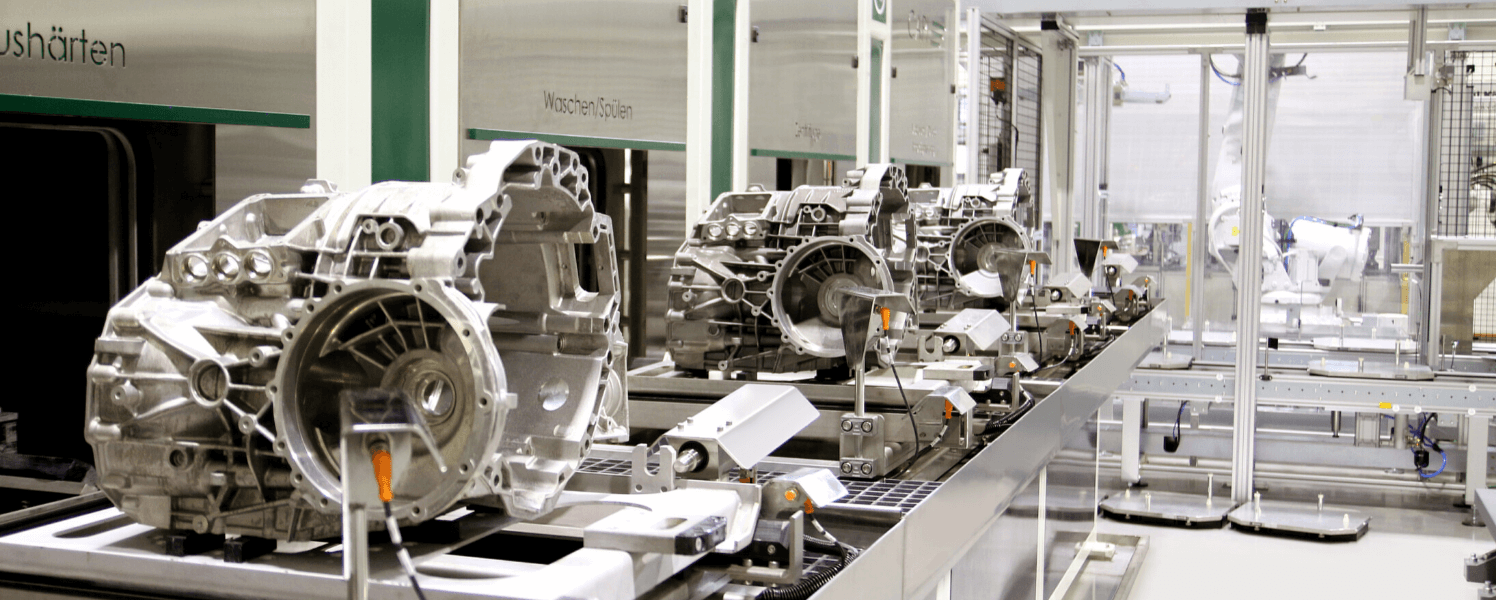
Myth: Vacuum Impregnation is a Cork or PlugFact: Vacuum impregnation seals porosity deep within the leak path; it is not a cork or plug. In the case of visible or open porosity, low viscosity sealants will most likely be washed out of pits or holes. Thus, a casting with surface porosity or blemishes before the process will exhibit the same surface porosity and blemishes after the process. However, the leak path below the part’s surface is fully sealed.
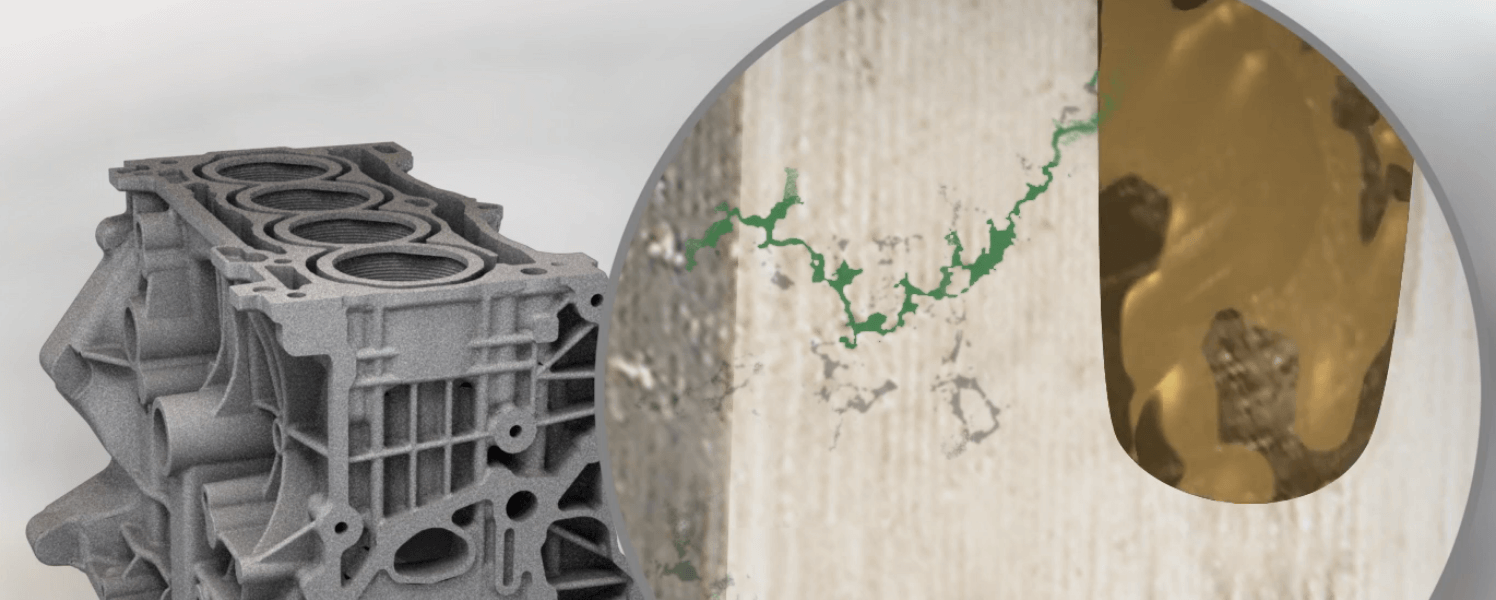
In Summary A clear understanding of how vacuum impregnation works can help companies maximize their production results. As the preferred method to prevent fluids or gases from leaking under pressure, the vacuum impregnation process seals casting porosity that forms during manufacturing. When done properly, the casting will function so that fluids or gasses will flow only where needed while physical characteristics, simply stated, will not be different in any manner. Vacuum impregnation helps manufacturers decrease the rate of scrapped parts, increase productivity, and ultimately increase their profitability.