A major breakthrough in impregnation technology that is proven to offer manufacturers clear-cut operational and performance advantages is now to be made available in the UK. American manufacturer, Godfrey & Wing Inc., believes the success achieved by its HVLV system in its home market and other parts of the world will be fully reflected by users in this country. The benefits of the system are now available nationwide through West Midlands surface finisher, Midland Impregnations Ltd., who are offering a dedicated subcontracting service.
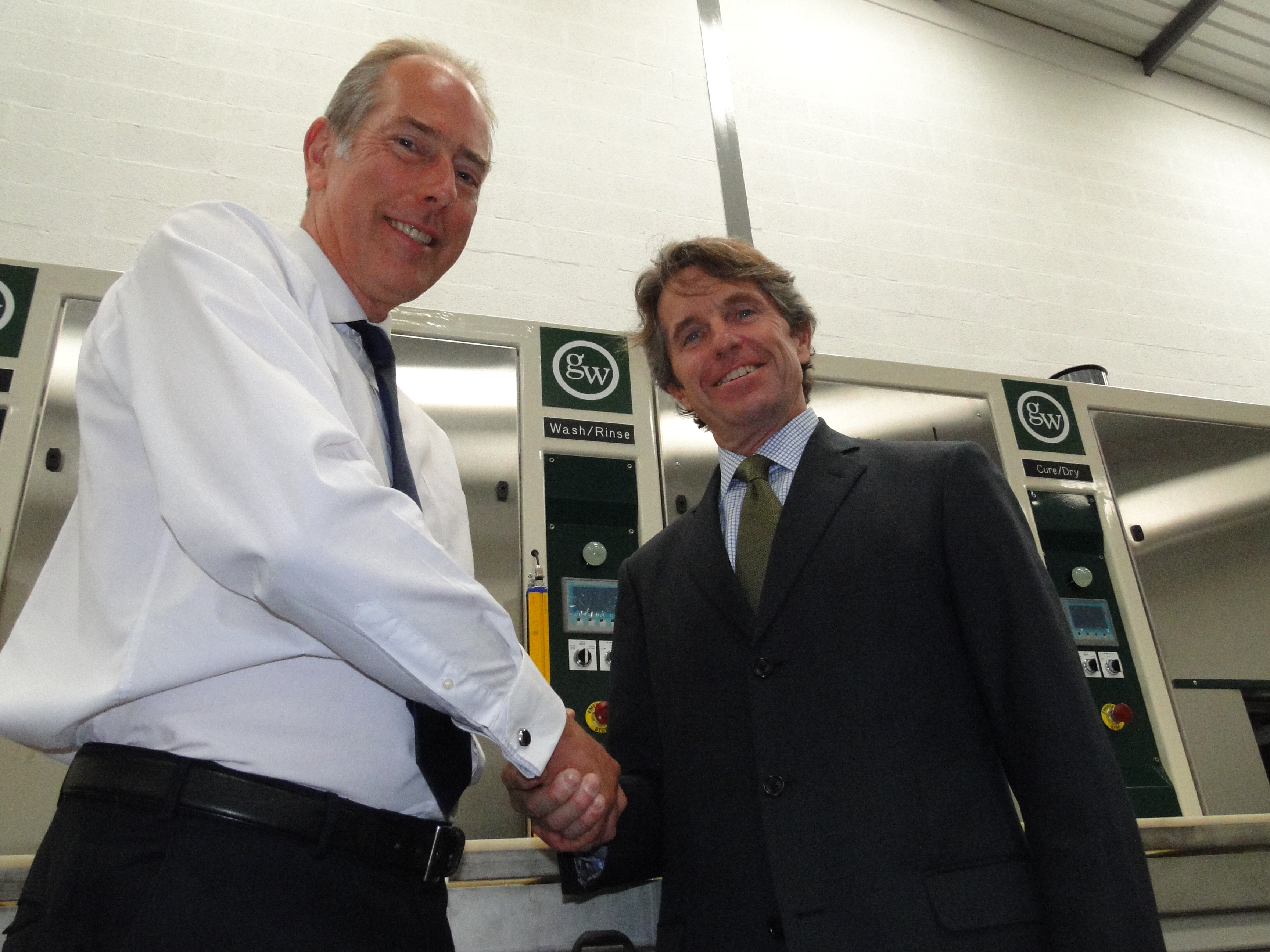
“Space savings, unmatched impregnation performance, dramatic cost reduction and environmental gains can all be achieved with the HVLV concept,” says Chris Gilmore, President of Godfrey & Wing. “We are seeing the benefits of the system with manufacturers in a range of industries – from the automotive and military sectors to general engineering, foundries and die-casters – all of which, of course, are highly active in the UK.”
The HVLV is centred on three frontloading operational stations which can be readily accessed by a single operator, with a link to a feed and discharge conveyor installed as needed. Up to 75% savings in floor area can be achieved compared with traditional impregnation installations which invariably have involved a gantry, catwalk, hoist and recessed equipment pit. The new HVLV design eradicates the need for this arrangement through a design that features both pressure and dry vacuum impregnation operations.
The capabilities of the HVLV are shown in its effectiveness in sealing porous materials. Sealing results exceeding 99% on micro-porosity in aluminium die-castings in a single pass are typical of the system’s capability while performance also gains from a centrifugal draining system that maximises sealant recovery. Complete cycle times as low as four minutes are achievable – up to a 90% saving against traditional methods.
“Components of varying sizes can be accommodated – from single units such as engine blocks, heads or transmission cases, to purpose-designed fixtures that can contain multiples of small items such as fuel pumps and aircon compressors,” continues Chris Gilmore. “Moreover, the HVLV unit is totally enclosed with an extraction system built in for fume extraction to maintain a clean working environment.”
With fully automatic operation, the system has been shown to interface efficiently with modern machine tools and manufacturing processes, enabling impregnation to become a genuine part of a production line. “This not only endorses the floor saving opportunities but also impacts directly on operational efficiency, opening up new opportunities in sectors such as advanced manufacturing,” adds Chris Gilmore.
With a proven track record worldwide, the introduction of the HVLV concept into the UK market is set to be of significance to a wide range of manufacturers and engineers. “The advantages of the system are now available via Midland Impregnations Ltd., located in Lye in the West Midlands, who are providing a subcontracting service to customers across the country,” adds Chris Gilmore. He also points out that MIL is happy to demonstrate the effectiveness of the process by impregnating sample castings, free of charge, for evaluation.
“We are delighted to be able to turn our attention to potential customers throughout the UK and are confident that they will gain from the benefits that are now well-established elsewhere,” continues Chris Gilmore. “Full details about the subcontracting arrangements in the UK market are now available on the Midland Impregnations website – www.midlandimpregnations.co.uk – while information on the HVLV system itself can be found via Godfrey & Wing’s office in Germany (+49 7131 40519-80) or via its USA website at www.godfreywing.com.”